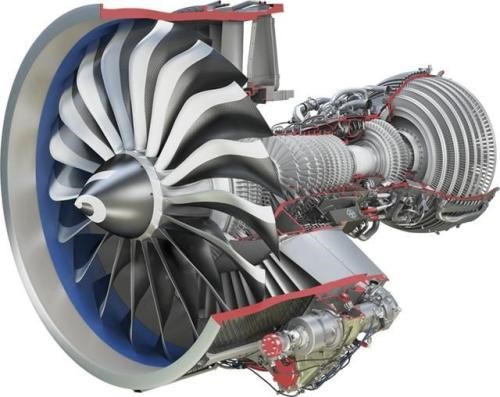
How can aircraft ensure safe flight in the sky? In fact, in addition to the engine, fuselage, wings, and elevators, there is also a seemingly inconspicuous accessory hidden in the structure that is very important. We call it the "balance weight." Some people believe that the lighter the aviation materials, the better. In fact, this is a partial view. Flying at high speeds at an altitude of several thousand meters, the aircraft faces unimaginable wind resistance and air pressure. The thin and weak body can only make the aircraft flutter in the wind, making it impossible to balance at all, let alone drive and control. Therefore, whether it is a passenger aircraft, a fighter jet, or a helicopter, it is necessary to add balance weights to major parts such as the wings, engine shaft, fuselage, tail, main shaft (helicopter), etc. to achieve balance and stability of the aircraft.
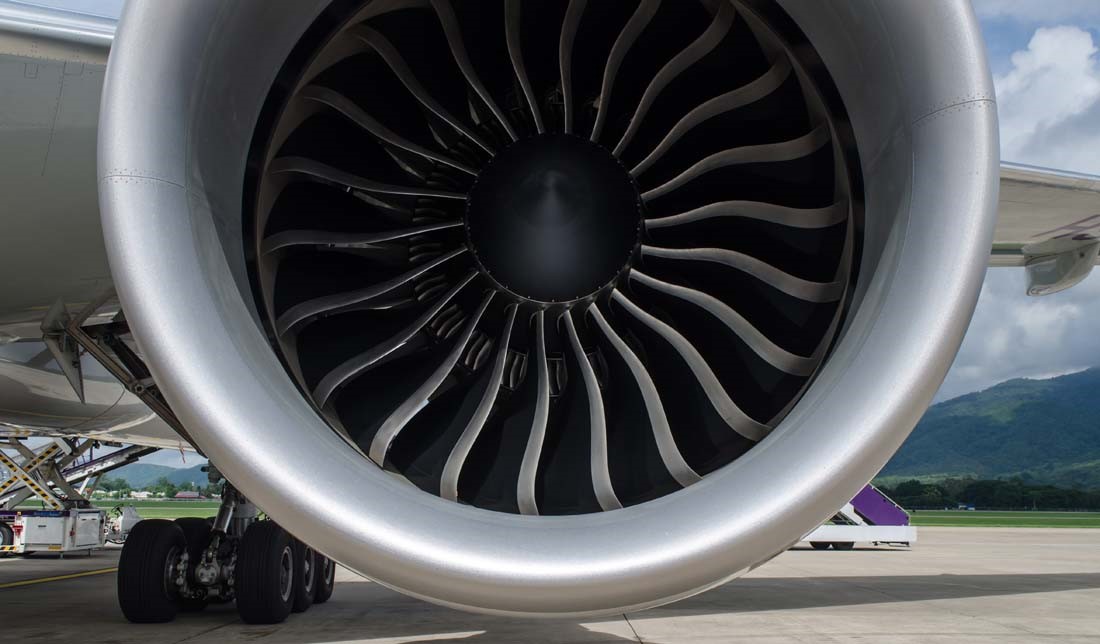
When a pilot flies an aircraft, the weight and g-forces on the ship affect the aircraft's safety, handling and performance. It is vital to maintain a stable center of gravity at all times to achieve perfect control and comply with flight safety standards. After taking into account the necessary onboard equipment, fuel and passengers, more weight must be added or distributed to bring the aircraft within the allowable weight range. In order to achieve this process, it is necessary to temporarily or permanently install a balancing weight. Aerospace counterweights can increase the sensitivity of the control mechanism and keep the aircraft operation within an acceptable range, increase weight, and maintain good stability and balance during high-speed flight.
Therefore, aircraft load balance is a key link to ensure flight safety. Selecting and optimizing the aircraft's counterweight and balance device can make full use of the aircraft's payload, save fuel, and improve air transportation efficiency. High-specific-gravity tungsten alloy is small in size, high in density, and easy to install and connect. It is a high-quality material for manufacturing aircraft counterweights and balance blocks. Typically used on all types of aircraft, including commercial and military aircraft. So why is tungsten alloy used in aviation balance weights?
While early aircraft counterweights were often made from toxic lead-containing materials, tungsten has become more popular in recent years due to its higher density at lower volumes. This refractory metal has a density of 18.75g/m3 and is about 50-60% heavier than lead. The resulting parts are only about 60% the size of corresponding lead parts of the same weight. This means that the volume of the ballast components can be reduced by 40%. Since aircraft have limited space, compact and dense ballast types are favored in the aerospace industry. Tungsten alloys have high density and small volume, which expands the possibilities for distribution within the aircraft, especially in the tail or nose areas of planes where space is limited.
In addition, tungsten alloy not only has the advantage of high density, but also has high strength and hardness, good thermal conductivity and weldability, good oxidation resistance, and small thermal expansion coefficient. It can also be used for aircraft load simulation during flight tests to facilitate Determine the precise location of ballast under different payload conditions. In short, tungsten alloy is currently the most effective material to balance the overall weight of the aircraft. Balance weight components made of tungsten are more likely to comply with AS9100 standards (AS9100 is an internationally recognized quality standard for the aerospace industry).
High specific gravity alloys made of tungsten are divided into W-Ni-Fe, W-Ni-Cu, W-WC-Cu, W-Ag, etc. according to alloy composition characteristics and uses. Their density is between 16.5-19.0g/cm3 , due to the need to mix in easily variable copper, nickel and gold metals, powder metallurgy is generally used to manufacture high-density alloys, and this type of process generally requires a sintering process. Although there is now 3D printing technology that can realize the manufacturing of tungsten alloy. However, tungsten is a refractory metal with a high melting point, so high-gravity alloy manufacturing still generally uses traditional methods. For example, the hydrogen reduction sintering method. This more traditional method of sintering high-specific gravity alloys is to install the green compact in a graphite boat or molybdenum boat and sinter it under hydrogen protection. In addition, there are vacuum sintering-isostatic pressing combined processes, sintering-hot isostatic pressing processes, etc.
Tungsten-based high specific gravity alloys are usually divided into temporary and permanent ones on aircraft. Temporary ballast is generally bolted to the structure of the aircraft and can be added and removed as needed. It is marked with its purpose and total weight. Once the temporary ballast is removed, the weight and balance of the aircraft must be checked again. The permanent balance parts must be fixed and labeled accordingly to prevent them from being accidentally removed from the aircraft. If someone really performs such a magical operation, the aircraft may cause unexpected problems due to lack of balance during navigation. s consequence.